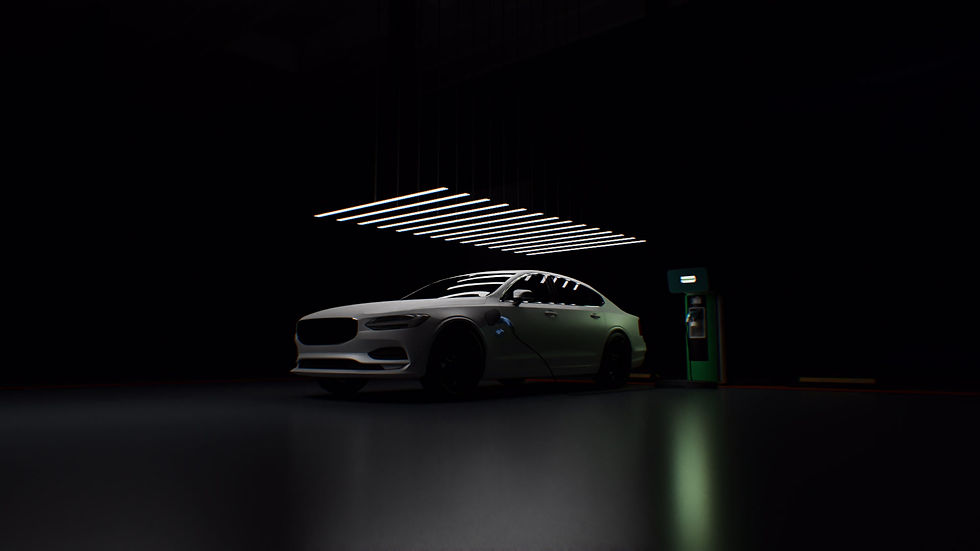
About PRIME
Li-ion Recycling Technology by ExPost
Purification and Regeneration Integrated Materials Engineering
What is PRIME?
PRIME recovers battery components and transforms them into their virgin states.
Purification and Regeneration Integrated Materials Engineering
Using Purification and Regeneration Integrated Materials Engineering (PRIME), we recover pristine quality battery components from battery scraps and end-of-life batteries. This scalable method, with its prominent economic, efficient, and eco-friendly process, has the potential to reshape the battery recycling industry.
Why not just mine more raw materials?
If recycling lithium batteries is so expensive and bad for the environment, why bother to recycle?
-
Environmental Impact: It is well known that mining can result in land-use change, habitat destruction, air/water pollution, GHG emissions, and a variety of other side effects. Recycling offers an opportunity for creating a circular economy and efficient reuse of limited resources.
-
Resource Preservation: Nickel, cobalt, and lithium reserves are finite. Recycling offers the possibility of multiple reuse of these valuable resources rather than depleting natural reserves.
-
Social Responsibility: Traditional mining operations often face opposition from local communities due to environmental and social concerns. By prioritizing recycling over extraction, we mitigate these issues and promote community well-being while meeting lithium battery demand sustainably.
-
Energy Efficiency: Although recycling by metallurgy can be as energy-intensive as traditional mining, our recycling approach consumes a lot less resources and generates lower emissions. This aligns with society's transition towards renewable energy.

What's wrong with current Li-ion Battery recycling methods?
-
Substantial CAPEX and OPEX Investment: Current recycling processes leverage traditional metallurgical techniques for extracting metals from scrap and spent batteries. These mining operations require large financial commitment and time to complete.
-
Long Processing Time: Through the metallurgical processes, batteries are broken down and transformed to raw materials/metals before synthesized into battery components. The process is not dissimilar to the production of new batteries from scratch.
-
Environmentally Unfriendly: Metallurgies involve the use of either fire or acid to melt the batteries before they go through the metal extraction process. Not surprisingly, they result in high energy consumption and/or GHG emissions.
-
Questionable Profitability for LFP and LMO: The economics of metallurgies are driven by the amount of precious metals, such as cobalt and nickel, that can be extracted from the processes. The lack of such metals in LFP and LMO challenges the economic viability of applying metallurgical techniques to these types of batteries.
How is PRIME different from traditional methods?
PRIME is an eco-friendly aqueous process using non-toxic and non-corrosive chemicals
The Old Way of Recycling Li-ion Batteries
The conventional recycling processes involve the use of fire or acid to melt and extract precious metals, such as cobalt and nickel in old batteries. These metals are subsequently reused in the manufacturing of new battery components such as cathodes and anodes. Hence, traditional recycling is akin to mining operation with old batteries replacing ores.
​
PRIME Technology
ExPost's approach diverges from this traditional method by avoiding the complete breakdown of the battery to its raw metal components. Instead, ExPost disassembles the batteries and revitalizes essential components like cathodes, anodes, and electrolytes to restore them to their original, pristine states. These rejuvenated components are then reintroduced into the production of new batteries. This streamlined process simplifies recycling significantly and better aligns with the core principles of recycling.